

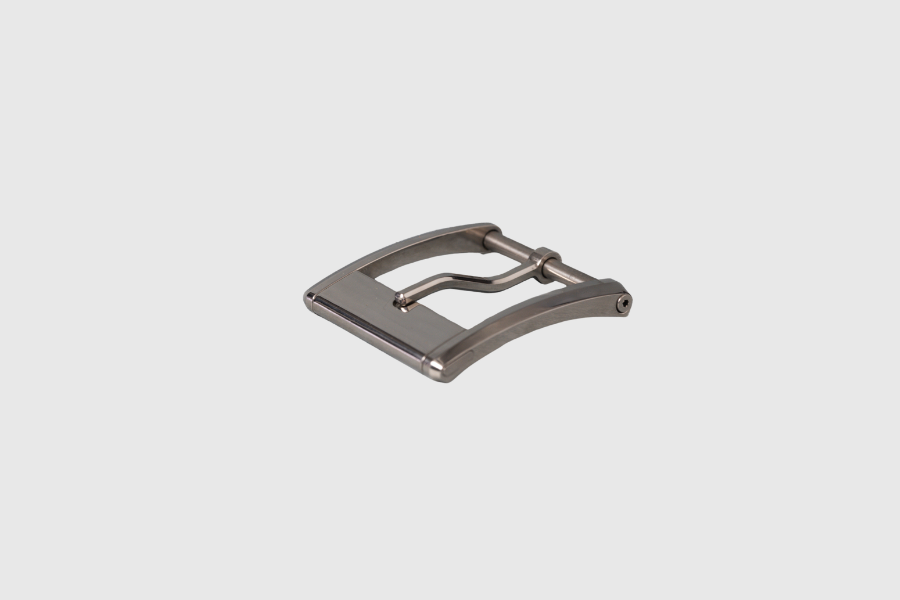
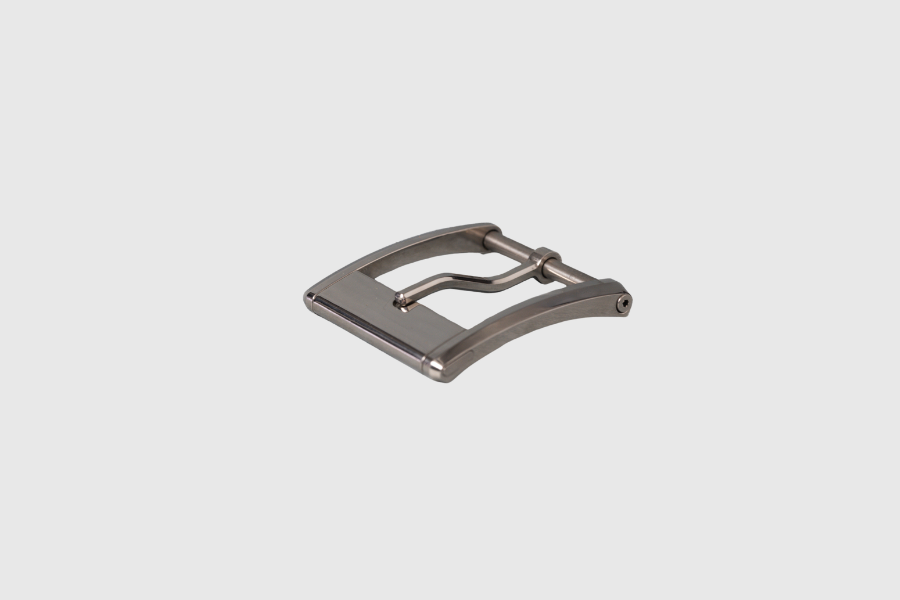
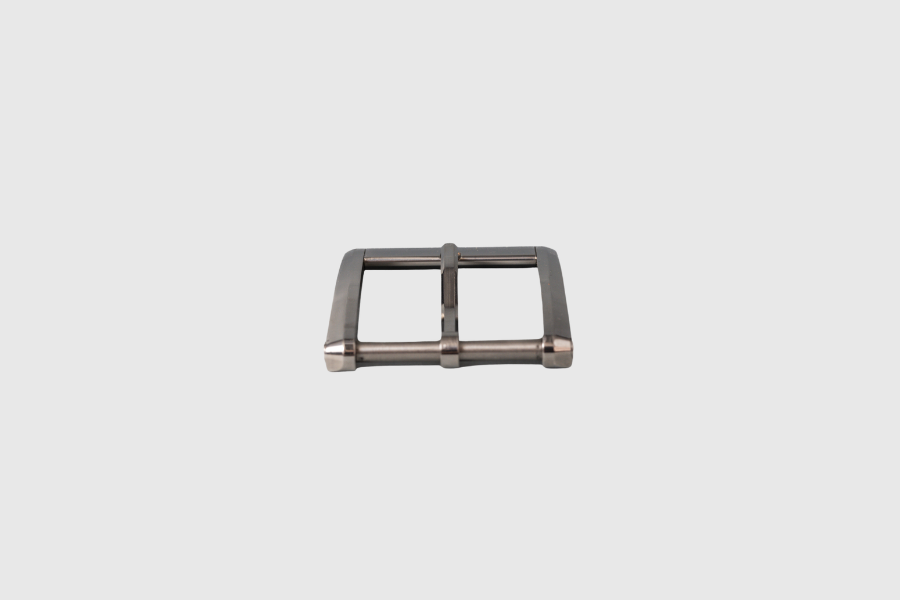
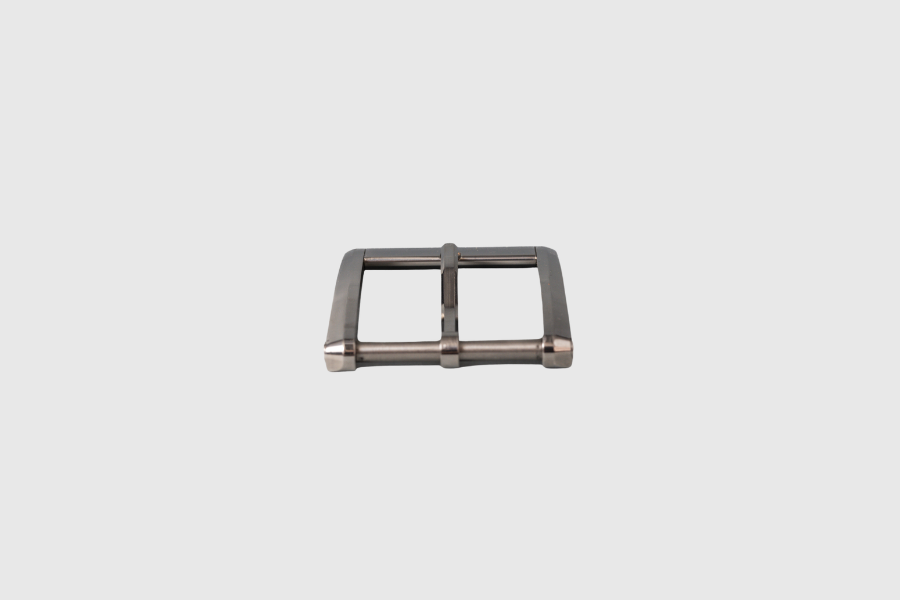

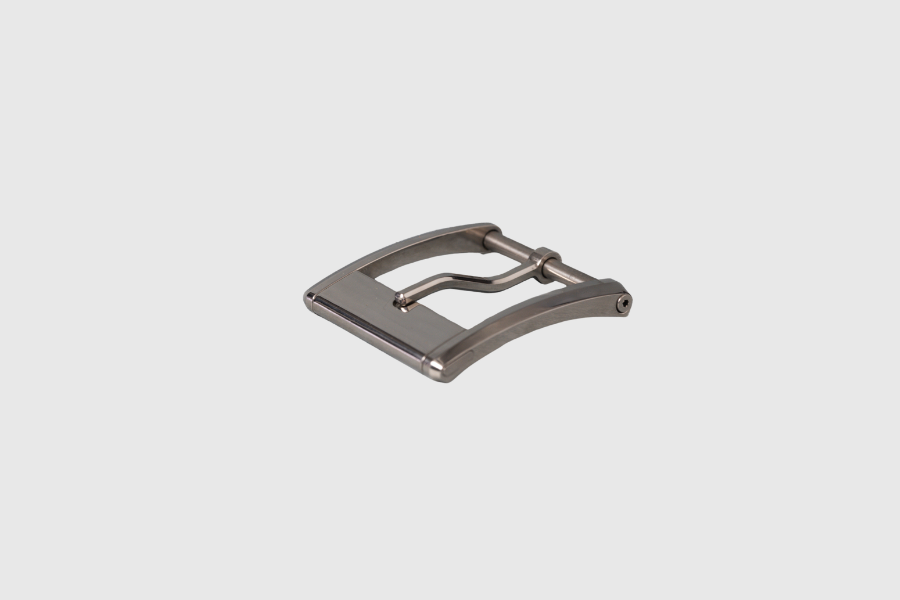
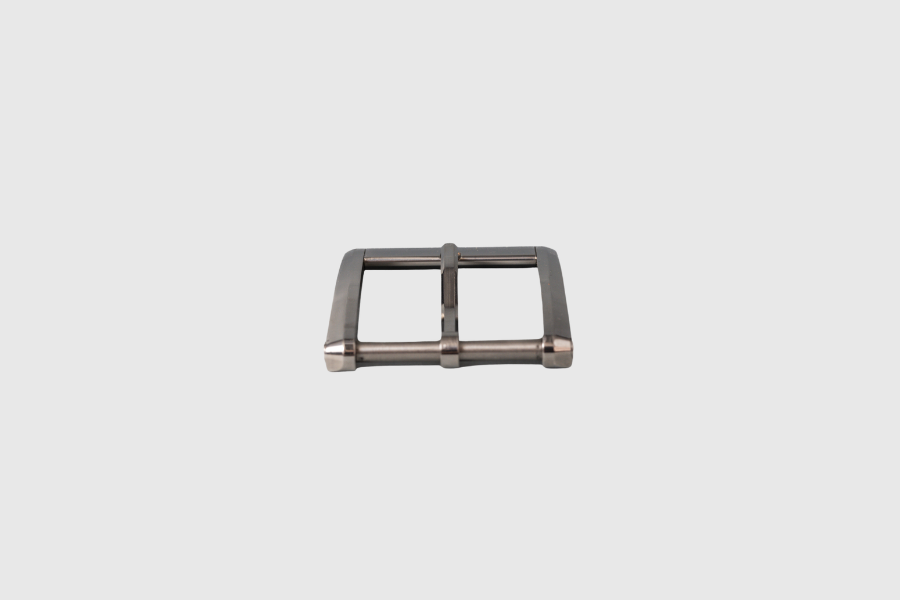
Belt Buckle - Polished Silver
Elevate your belt with this CNC milled, Stainless Steel belt buckle. Crafted with precision and elegance, this buckle combines unparalleled durability with a timeless design that effortlessly elevates any outfit.
Belt buckles are often a statement piece, and this one is no different. Beautiful geometry coupled with precise chamfers produce perfect lines more closely resembling a foreign car than a casual buckle. You may be convinced to place this in a showcase instead of on a belt.
Made from 100% Stainless Steel
Powder Coated for added durability
Precision milled to allow for unique features
Fits 1.5” belts
Elevate your belt with this CNC milled, Stainless Steel belt buckle. Crafted with precision and elegance, this buckle combines unparalleled durability with a timeless design that effortlessly elevates any outfit.
Belt buckles are often a statement piece, and this one is no different. Beautiful geometry coupled with precise chamfers produce perfect lines more closely resembling a foreign car than a casual buckle. You may be convinced to place this in a showcase instead of on a belt.
Made from 100% Stainless Steel
Powder Coated for added durability
Precision milled to allow for unique features
Fits 1.5” belts
Elevate your belt with this CNC milled, Stainless Steel belt buckle. Crafted with precision and elegance, this buckle combines unparalleled durability with a timeless design that effortlessly elevates any outfit.
Belt buckles are often a statement piece, and this one is no different. Beautiful geometry coupled with precise chamfers produce perfect lines more closely resembling a foreign car than a casual buckle. You may be convinced to place this in a showcase instead of on a belt.
Made from 100% Stainless Steel
Powder Coated for added durability
Precision milled to allow for unique features
Fits 1.5” belts
History
End mill machining is the process of using a cutting tool called an end mill to shape and remove material from a workpiece. The end mill rotates and cuts into the workpiece, creating features such as flat surfaces, slots, contours, pockets, and drilled holes. It is commonly used in milling machines to shape various materials with precision.
End mill machining has its roots in ancient times when early civilizations used manual milling techniques to shape and cut various materials. The use of rudimentary tools like hand mills and rotary files allowed for basic milling operations, albeit with limited precision and efficiency.
The Industrial Revolution in the 18th and 19th centuries brought significant advancements to milling technology. During this era, the development of powered machinery, such as watermills and steam-driven mills, transformed milling into a mechanized process. These early mills utilized simple cutting tools like rotary cutters and fly cutters to perform milling operations.
As the Industrial Revolution progressed, the demand for more accurate and versatile milling tools increased. In the mid-19th century, the invention of the milling machine by Eli Whitney (or maybe Robert Johnson of Middletown) and others revolutionized milling operations. These early milling machines allowed for the precise movement of workpieces relative to cutting tools, enabling more intricate and controlled machining.
The introduction of high-speed steel (HSS) in the late 19th century further improved milling capabilities. HSS end mills offered enhanced hardness and heat resistance, enabling faster cutting speeds and greater durability. This development significantly expanded the range of materials that could be machined effectively.
In the mid-20th century, the emergence of carbide cutting tools marked another significant milestone in end mill machining. Carbide end mills, made from a combination of tungsten carbide particles and a binder material, provided even greater hardness and wear resistance than HSS. This allowed for higher cutting speeds and longer tool life, contributing to improved productivity and efficiency.
The advent of computer numerical control (CNC) machining in the mid-20th century brought about a revolution in end mill machining. CNC machines, controlled by computer programs, enabled precise and automated milling operations. This technology opened up new possibilities for complex geometries, 3D machining, and high-speed machining, as well as improved repeatability and accuracy.
In recent years, advancements in coatings, tool geometries, and cutting edge designs have further enhanced the performance of end mills. Advanced coatings like titanium nitride (TiN), titanium carbonitride (TiCN), and aluminum titanium nitride (AlTiN) provide increased tool life, reduced friction, and improved chip evacuation. Specialized end mill designs, such as ball nose end mills and variable helix end mills, have been developed to cater to specific machining needs.
Today, end mill machining plays a vital role in numerous industries, including aerospace, automotive, mold making, and general machining. It allows for the precise shaping and cutting of various materials, ranging from metals to plastics and composites.
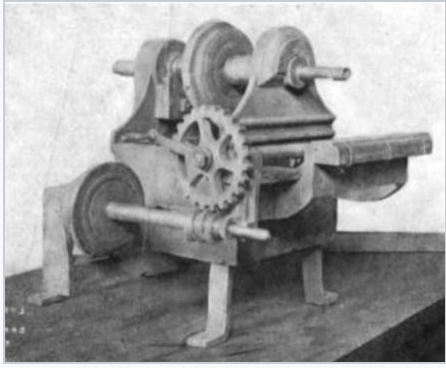
The first milling machine, possibly created by Eli Whitney